Tassie to lead world in electric powered ferries
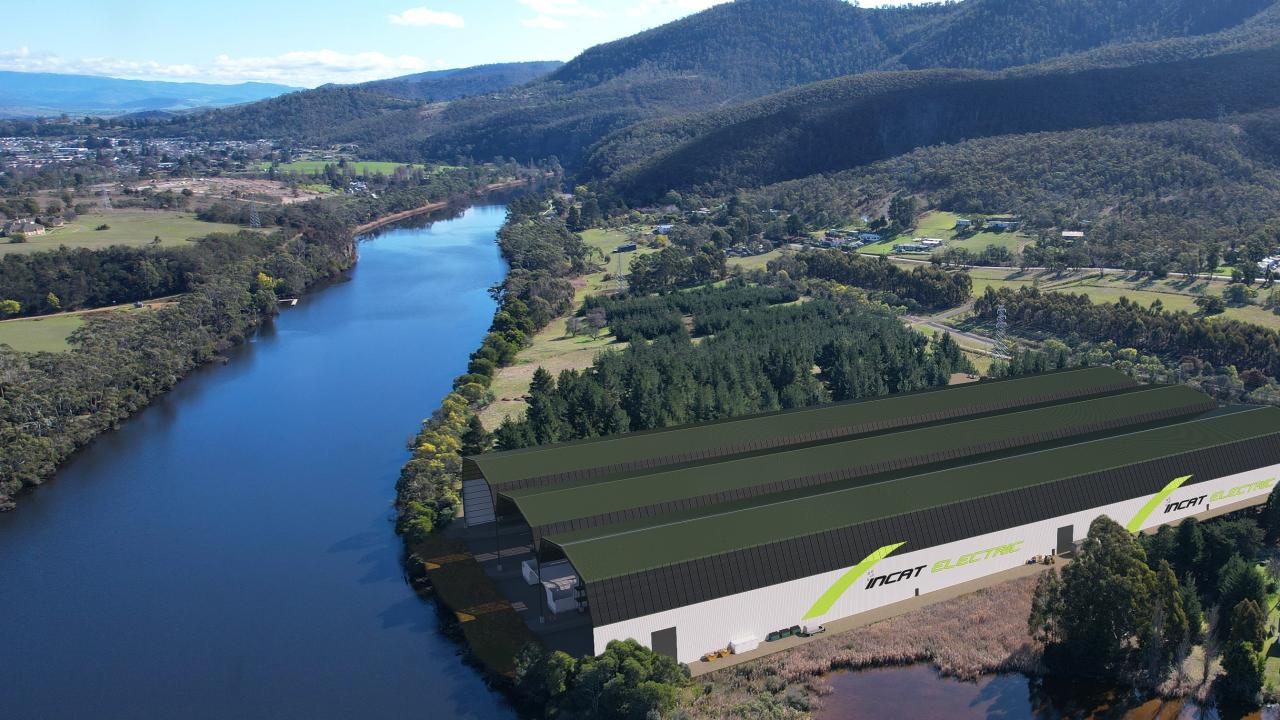
Picture: An artist's rendering of the new ship building Incat plans for Boyer.
BOB Clifford clambers over and under the four decks of this ferry as fluidly as the clusters of tradies and techs bringing life to the all-electric water-skimming behemoth here at Incat’s Hobart shipyard.
He may be 80 now, with 10 years elapsed since he moved from a CEO role to that of chairman, but he remains deeply involved in the day-to-day operations of this place and the ships it builds.
Over the day, he’ll likely make two circuits of this Ro-Pax (passenger-car) vessel, a $US 150 million commission that will carry 270 vehicles and more than 2000 passengers out of Buenos Aires.
For South America’s Buquebus company, here is the largest lightweight battery electric ship so far constructed in the world, with an energy storage system of over 40MWh, four times larger than any comparable vessel.
Below the wheelhouse where we’re standing is a chunk of space devoted to passenger comforts and duty free, with a vehicle deck underneath that.
Lower still is a 400-tonne battery-electric system driving eight water jets needed to shove the massive craft through the waves.
That future is electric ferries, he tells the Gazette, and he sees a world market for more than 1,000 of vessels like this one.
“We could build at least four of them here in Tasmania,” he says quickly. “We’ve got the capacity, the tech and the talent working in aluminium to build superstrong vessels that are world-class.”
The decision to add that shipbuilding capacity at Boyer, 30 kilometres upriver from this facility, is being announced by Incat this week.
Three new production sheds are proposed on the water’s edge on the New Norfolk side of the paper plant.
They’ll open to the southern side, onto the Derwent, so that completed hulls can be sailed the 30 kilometres downstream to the Incat sheds at Prince of Wales Bay for installation of its innards.
“We can add a little more capacity here, but essentially, we’ve run out of room,” he says, indicating the steeply sloped limits of the PoW site.
He notes the vessel beneath our feet is 27 metres wide and 130 metres long, as large a vessel as can be accommodated in the largest of Incat’s current construction sheds.
“What I’ve been looking for, and found at Boyer, is a very specific combination: it’s a gentle slope to the water, and enough depth so we can float the hull downriver and pass underneath the two bridges. You can’t move 2,000 tonnes by road.”
He’s referring to the Bowen and new Bridgewater Bridge, both of which have 16.2 metres of headroom. “With Boyer, we’ve found that sweet spot,” he adds.
Clifford moves to the subject of the market for electric ferries, those able to travel about 160 kilometres, which is well within current technological capabilities.
“We’ve got to be ready for what’s coming, initially Europe and South America. While Australia is currently behind the curve, within a short space of time Sydney Harbour is going to need 50 ferries and probably the Barrier Reef too.
“That suits us very well in terms of the size of vessel we specialize in, sets up a huge market for us.”
And with New Norfolk now in the mix, Incat will have further access to a skilled workforce, the tradespeople able to deliver the ferries it wants to build.
And Mr Clifford stresses: “These a long-term, high quality jobs, jobs for life,” he says. It’s an old-school concept, but that’s the place he comes from.
About half the work, on the hull and decks, can be done at Boyer, and the remainder, including engines and batteries, at the current site.
And Incat is already talking with potential customers. He points out that the battery charging infrastructure needed at most ports is yet to be built, but the lag time provides a window for shipbuilders to get to work on the vessels themselves.
“Dover and the English Channel run is going to need about 100 megawatts,” he says. “It currently has eight.”
As he has for much of the half-century he’s been building ferries, Bob Clifford talks knowledgeably, even fondly, about aluminium as the core fabric of his vessels. From cross-beams to composites, stairs to shaped hulls, he attributes much to aluminium’s myriad properties.
It’s the reason for the company’s longevity and success.
“Aluminium is less than half the weight of steel, which means faster speeds from smaller engines, lower operating costs and quicker turnarounds,” he says.
“And the shift to electric engines moves the dial further in that direction, the way we’re already travelling,” he told the Gazette.
Add new comment